OptiPro
Optical Precision Technology for Integrated Low-Cost Robot Handling and Part Orientation
Subject of research
Currently, a range of low-cost robotic systems are available on the market. IGUS offers articulated industrial robots and cobots with reach up to 1 meter and payloads of up to 5 kg for less than €5,000. The positioning repeatability is in the range of +/-0.5 mm. The systems from Fruitcore Robotics have a minimum repeatability of +/-0.05 mm. The prices range from €10,000 to €20,000, which is 2 to 3 times lower than industrial robots from established providers or cobots from Universal Robots. For high-precision processing tasks such as polishing processes or laser engraving tasks with stringent accuracy requirements, these systems are unsuitable due to their imprecise positioning. Laser engraving of reference patterns for calibration tasks or applying scales requires an absolute accuracy of up to +/- 5 μm. The use of fine positioning units in the form of stepper motors for tracking significantly increases the weight of the gripper and requires a highly accurate measurement system to determine the current positioning deviation. Often, the approach taken is for the robot to place the part into a component-specific, highly accurate fit of a fixture. However, this involves a high manufacturing cost for the production of highly accurate fixtures for each part and is only economically viable for large-scale production. This solution is unsuitable for single-part production, small batches, and the associated need for flexibility.
Project goal
The goal is to compensate for the positioning error of robotic systems used for the positioning of locally highly precise geometric elements (e.g., laser processing) without the need for high-precision linear or rotary axes or fixtures for component positioning. As part of the project, a novel measurement system will be developed to determine component positions in the context of robot-assisted precision processing. The result will be a retrofit kit for existing processing systems. The aim is to enable highly precise labeling or processing of components using any (low-cost) robotic system, which has an absolute positioning accuracy of up to +/- 1 mm, with a lateral accuracy of around 1 µm, by capturing the positioning error and actively correcting it through the processing system.
Component Project Title
Optical Precision Technology for Integrated Low-Cost Robot Handling and Part Orientation
Implementation
- Selection of a suitable handling robot
- Selection of a suitable sensor for capturing the component geometry and position
- Selection of an appropriate camera with telecentric optics
- Integration of the sensors into the demonstrator system based on a laser engraving system
- Development of algorithms for 3D position determination of the component
- Development of algorithms for precise determination of the laser’s workplane position
- Development of methods for calculating correction values and transferring them to the laser engraving device and handling robot
- Establishment of communication between all involved automation systems
- Integration of all program routines into a unified program with GUI
Verbundkoordinator
GFE Präzisionstechnik GmbH
f.schroedel@hs-sm.de
Näherstiller Str. 10
98574 Schmalkalden
Contact person
Prof. Dr.-Ing. Frank Schrödel
Schmalkalden University of Applied Sciences
Blechhammer 9
98574 Schmalkalden
+49 (0)3683 688-2107
Additional Information
- Project Duration: January 1, 2025 – December 31, 2026
- Subproject Budget: €0.22 million
- pdf (german): OptiPro - Optical Precision Technology for Integrated Low-Cost Robot Handling and Part Orientation
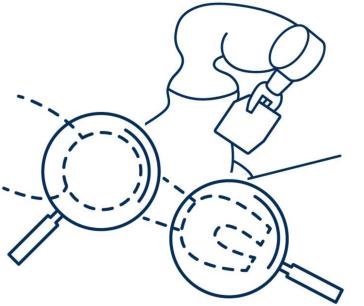