3D-FMM
Development of a modular and scalable 3D coordinate production measurement platform
Subject of research
In modern manufacturing, precise dimensional measurements are crucial for quality assurance. Conventional coordinate measuring machines (CMMs) require separate measurement procedures outside the production line, leading to increased cycle times and potential production bottlenecks. The aim of this project is to develop an inline measurement solution that can be directly integrated into the production process, rendering traditional measuring devices unnecessary. A collaborative robot (cobot), equipped with a tactile probe as an end effector, will be used to measure product dimensions within the production line. One of the main challenges when using robotic arms for precision measurement lies in their inherent, manufacturer-certified accuracy limits. Although the robot hardware has the potential for higher accuracy, its certified precision is often insufficient for high-precision measurement tasks. To overcome this limitation, we will employ software optimization techniques to enhance the robot’s precision and ensure compliance with the required measurement standards. The system must achieve a measurement accuracy of ±0.01 mm at a speed of approximately 35 points per 1.5 minutes. To accurately determine the coordinates of each point, two different measurement methods will be used. The system must operate within a workspace of 2000 x 2000 x 1000 mm. By analyzing measurement data across multiple components, the system will be able to detect error trends and provide critical feedback for the calibration of production equipment. This feedback loop will help minimize deviations and improve the overall precision and efficiency of the manufacturing process.
Project goal
The goal of this project is to develop a software-based compensation system for positioning errors in robotic systems used for inline measurement. This system will enable highly precise dimensional measurements without the need for high-precision linear or rotary axes or specialized positioning devices.
An innovative measurement method will be implemented to accurately determine the position of components within the production line and to correct positioning errors in real time. The developed system is intended as a retrofit solution for existing production environments and utilizes a cost-effective cobot system with an absolute positioning accuracy of up to ±0.03 mm.
Through software-based optimization techniques, the measurement accuracy will be improved to achieve a lateral precision of approximately 10 µm, ensuring reliable, high-precision measurements and effective process control.
Implementation
- Selection of a suitable robot
- Selection of a suitable tactile sensor for dimensional measurement
- Integration of sensors into the measurement system
- Development of algorithms for 3D position determination
- Development of algorithms for measuring measurement errors
- Calculation and application of correction values
- Integration and communication between automation systems
- Development of an integrated software system with GUI
Project Consortium Coordinator
PREMETEC Automation GmbH
info@premetec.de
Sommerbergstraße 42
98527 Suhl
Contact person
Prof. Dr.-Ing. Frank Schrödel
Schmalkalden University of Applied Sciences
Blechhammer 9
98574 Schmalkalden
+49 (0)3683 688-2107
Additional information
- Project Duration: January 14, 2025 – January 12, 2026
- Subproject Budget: €0.25 million
- pdf (german): 3D-FMM - Entwicklung einer modularen und skalierbaren 3DKoordinaten- Fertigungsmessplattform
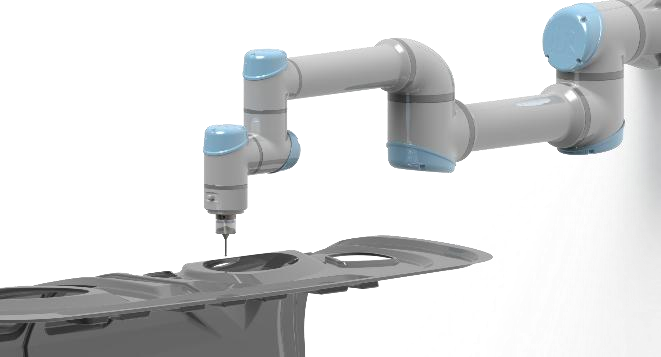